Управление качеством — новый взгляд
20 Ноя 2009 Вячеслав Марков и Павел Рабунец в рубрике Lean в России и мире, Рекомендуем | 5 комментариев
Просмотров: 6 406
Качество! Качество продукции, качество работы, качество услуги… Как должна быть налажена работа по управлению качеством на производстве? Может ли продукт быть качественным лишь частично? Мы полагаем, что качество не может быть половинчатым — либо продукт качественный, либо нет.
Поэтому главный вопрос, которым следует ежедневно задаваться менеджменту современного предприятия: «Как обеспечить 100%-ное качество продукции?».
В то же время «качество» в руках не подержишь, и каждый понимает значение этого слова по-своему. Необходимо ясно представлять, что истинная цель управления качеством — не само управление, а именно качество конечного продукта и удовлетворение потребителя.
Качество — это не услуга или функция продукта, добавляемая на одном из этапов его производства. Это обязательная составляющая — результат правильного процесса создания ценности, и результат правильной работы всего персонала предприятия. Чтобы разобраться в этом, давайте вспомним, как «создают качество» в бережливых компаниях и поговорим о том, как это делают на Ваших и других российских предприятиях.
Для современных промышленных производств изготовление качественной продукции, отвечающей постоянно возрастающим требованиям, становится всё более важной задачей. Актуальность этой задачи также подтверждается практикой лучших японских компаний, показывающих на своём примере, что гораздо эффективнее и дешевле обеспечить качество на рабочем месте с первого раза и не допустить передачу проблемной продукции дальше по ходу производственного потока, чем заниматься проверкой качества готовых изделий и исправлением дефектов пост-фактум.
Значительных успехов в обеспечении высокого качества продукции и во внедрении принципиально новой системы встраивания качества в процессы производства автомобилей достигла компания Toyota.
В основе системы лежит идея получения стопроцентного качества продукции в любое время на протяжении всего производственного процесса и без необходимости дальнейшего контроля качества. Главная цель системы встраивания качества, получившей название «дзидока» — делать скрытые производственные проблемы явными и немедленно привлекать внимание к каждой проблеме, потому что скрытые проблемы достаточно сложно разрешить. «Дзидока» реализуется в незамедлительной остановке производственного процесса при возникновении проблемных ситуаций ради встраивания качества в процесс и состоит из двух принципов:
- Принцип автоматической остановки оборудования при возникновении любых отклонений от нормального течения технологического процесса.
- Принцип ручной остановки процесса с использованием сигнальной системы «андон».
Согласно первому принципу «дзидока» также называют «автономизацией», то есть наделением оборудования человеческим интеллектом, что выражается в оснащении технологических линий специальными устройствами, которые обнаруживают любые проблемы и отклонения, в результате чего станки останавливаются автоматически.
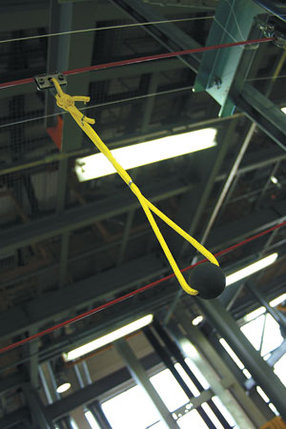
Андон
Для ручной остановки всей технологической линии или её отдельного участка используется сигнальная система андон (в переводе с японского означает «сигнал, зовущий на помощь») в виде специальных пультов остановки или шнуров, расположенных на рабочих позициях. Любой работник может с помощью «андон» остановить линию в том случае, если он заметил отклонение от стандартного хода процесса или операции, и таким способом на весь производственный персонал возлагается ответственность за качество. «Андон» устраивается определённым образом, чтобы персонал, отвечающий за оказание помощи, мог быстро и точно определить рабочее место, на котором возникла проблема. В момент остановки оборудования флажки или световая индикация, сопровождаемая звуковыми сигналами, оповещает всех участников процесса, что на данном участке требуется помощь для устранения проблемной ситуации. В определённых случаях «андон» сигнализирует о риске появления проблемных ситуаций с качеством, из-за которых производственная линия будет остановлена. Например, практически на всех сборочных линиях заводов компании Toyota у персонала есть 5-30 секунд до остановки оборудования, для того чтобы быстро решить проблему или обнаружить, что проблему можно решить без остановки линии.
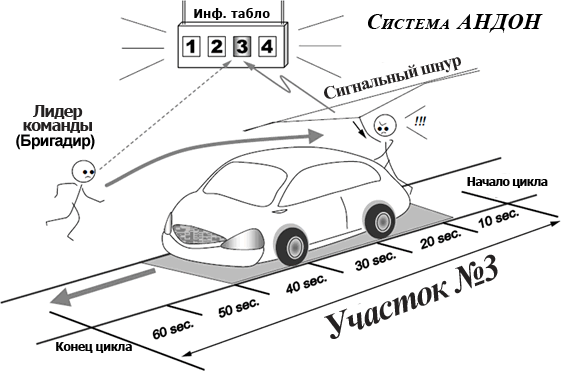
Демонстрация системы андон: рабочий на участке №3 замечает отклонение от стандарта или неисправность и останавливает линию, дергая сигнальный шнур. На информационном табло отображаются главные параметры работы системы андон. Горящая лампа №3 говорит о том, что именно на 3-ем участке возникла проблема. Лидер команды (бригадир, тим-лидер) спешит именно к этому участку.
Для оперативного решения проблем с качеством и пуска оборудования в работу производственному персоналу следует делегировать полномочия принятия решений без обращения к руководящему составу, а также предоставить необходимые инструменты и ресурсы. Как только проблемная ситуация будет диагностирована и устранена, оборудование без промедлений запускается в работу.
Ещё одним элементом системы встраивания качества является то, что каждая рабочая позиция оснащена методами и устройствами для предупреждения ошибок, называемых «пока-ёке», которые исключают возможность рабочему совершить ошибку. Эти устройства представляют собой фотоэлементы, фиксаторы, ограничители и другие простые механизмы, препятствующие отклонению от стандартных процедур и появлению дефектной продукции.
Таким образом, в сравнении с традиционными методами обеспечения качества продукции на основе статистического анализа, по нашему мнению, именно остановка производства с целью решения оперативных проблем в сочетании с встраиванием качества в производственные процессы современных промышленных предприятий позволяет достичь стопроцентного уровня качества готовой продукции без необходимости последующего контроля и способствует формированию производственной культуры, ориентированной на создание качественной продукции с первого раза.
Об авторах:
Подписывайтесь на Leaninfo.ru в соцсетях:
Или следите за новостями бережливого производства по email.
Смотрите также:
Оставить комментарий
Для отправки комментария вам необходимо авторизоваться.
Комментарий к статье от моей коллеги – маркетолога Екатерины Челищевой (один из авторов письма президенту), не изучавшей ранее принципы и производственную систему Toyota:
«Я видела такие системы (шнуры для остановки линии) во время экскурсии по немецкому заводу Audi. Впечатляет. Но эта ежедневная борьба рабочих завода за качество полностью опирается на культуру производства. В Германии рабочий-заводчанин имеет престижный и уважаемый в обществе статус. А в нашей стране какое традиционное отношение к работягам?»
Правильно… такое, как Вы и подумали…
Школьники и студенты мечтают стать в будущем юристами, бухгалтерами, экономистами, работниками гос. бюджетной сферы и т.д. Возникает вполне логичный вопрос: А кто будет создавать добавленную ценность российским товарам? Это огромная проблема, не решив которую товары с надписью «made in Russia» никогда не станут конкурентоспособными и популярными на мировых рынках!!!
Безусловно, современные реалии требуют эффективной системы мотивации персонала. Необходимо, чтобы профессия рабочего стала уважаемой в нашей стране, чтобы каждый россиянин проникся тем, что он работает на благо страны, создавая российские товары.
Для этого необходимо как постепенное изменение сложившегося мнения специалистами на конкретных предприятиях, так и поддержка на самом высоком уровне. Хотелось бы слышать от президента России и председателя правительства РФ слова о необходимости рабочих профессий в цепочке создания ценности.
«Таким образом, в сравнении с традиционными методами обеспечения качества продукции на основе статистического анализа, по нашему мнению, именно остановка производства с целью решения оперативных проблем в сочетании с встраиванием качества в производственные процессы современных промышленных предприятий позволяет достичь стопроцентного уровня качества готовой продукции…» Супер! И какие же японцы умные! Веревку повесили и сразу Toyota сошла с конвейера. Все дело-то в веревке! Господа и дамы! Не будте невежественными. Изучайте классику. Эта система действует в Японии только потому, что статистическое управление процессами позволяет таким образом реагировать на особые причины возникновения дефектов. А Вы — веревкой, да еще 100% качество. Веревкой ни УАЗ, ни КАМАЗ, ни Автоваз ни любой другой АЗ не спасешь. Скорее угробишь.
На УАЗе веревки конечно нет. Но зато есть кнопки останова конвейера. Одна кнопка на 10 рабочих мест примерно. И конвейер останавливается, если возникает проблема. Проблему решают оперативно. Эти кнопки, кстати, функционируют еще с советских времен. В основном остановка конвейера происходит из-за нестыковки отверстий в узлах, например, рамы и кузова. Эта нестыковка происходит из-за износа сварочных кондукторов.
Остановка конвейера на УАЗе происходит редко. Все детали и узлы проходят контроль, прежде, чем попасть на сборку. Для качественного контроля у УАЗа всё есть.
Андрей, вы всё восприняли буквально. В посте говорится о концепции встраивании качества в производственный процесс. Это ведь больное место для нашего автопрома, не правда ли? И умело применять этот подход там пока не научились.
Лично я воспринимаю Производственную Систему Тойоты, как классику. Если глубже копнуть, обратившись к трудам Сигео Синго, то можно узреть, что именно стремление достичь 100%-ного качества на японских предприятиях, стало стимулом к останове процесса для решения проблемы на месте. А статистические методы, по убеждению японских производственников, с этой задачей не справлялись.